Learning Journeys Japan
Lean Production and Leadership – OPERATIONAL EXCELLENCE of Companies in Japan
Nothing is more inspirational than experiencing successful role models. And nobody moves more than inspired managers. That's why we offer
- 'Learning Journeys to the Sources of Excellence': to Japan, to the origins of TPS, LEAN and Kaizen
- Quality over quantity: Four to five visits to companies regarded in Japan as benchmarks for Monozukuri®Monozukuri – i.e. the manufacturing of things
- In-depth visits: Extensive factory tours, including live presentations of Kaizen activities; these visits are sometimes much longer than the typical 2-hour visits organised by other operators
- Focus on the how: One-day Kaizen training session led by former Toyota TPS trainers – with guaranteed aha! effects for all participants
- Impactful encounters: with 'LEAN Leaders' and 'Kaizen Managers' – insight into their 'toolboxes' and how they approach leadership in practice
- Rigorous evaluation directly in Japan: Analysing the differences and the LEAN success factors
- Team and network building among the participants as a desirable side effect
The main topics are LEAN Production and Kaizen in application as well as the leadership required in this process. Former top managers explain how this works in a webinar, which is an integral part of the learning journey:
- Corporate culture, mindset and how to change them: Insights gained from successful corporate reforms (more here)
In addition, we train the participants in a preparatory seminar on the differences between TPS and LEAN as well as Japan's economy, society and culture
The aim is to give the improvement process in your company a powerful and sustainable boost. The standard by which the learning journeys are to be measured is: Ultimately, the only thing that counts is what is later implemented in your own company. Whether we live up to this claim you can see here.
What our Participants say:
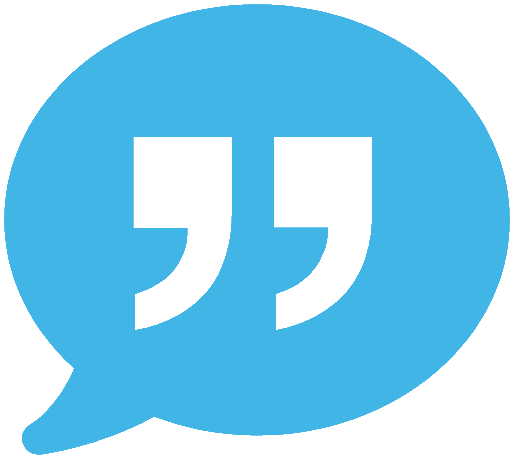
Our goal was to reinforce the knowledge of the methodology, to go deeper into the real meaning of the kaizen culture and to go beyond the tools by visiting the actual places where it was born, grown and developed.
The journey has revealed as a full and intensive experience, from practicing the kata with our hands, by sharpening knives, till visiting companies which are applying the philosophy which is embedded in the processes and most of all in the people.
The trip itself was prepared, organized and managed very well. Roman Ditzer has a deep understanding of how TPS and kaizen actually work in Japanese firms, his extensive experience helps to capture the full meaning of the discussions which is not a given considering the cultural and language differences. From the standpoint of fischer Consulting we can just say that to get the most out of the Lean 'essence' it is mandatory to go beyond the tools and the Learning Journey shows you what’s the beyond.
What our Participants say:
What our Participants say:
What our Participants say:
What our Participants say:
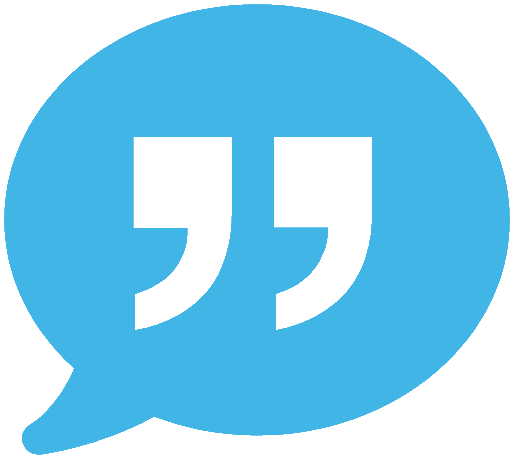
The Pathway to OPERATIONAL EXCELLENCE Goes via Japan.
Why Japan?
The 'Executive Summary on 12 slides' (PDF) illustrates the connection between Kaizen and OPERATIONAL EXCELLENCE, as well as the importance of the soft factors: mindset and leadership. A more detailed explanation of the connections can be found on the following slides.
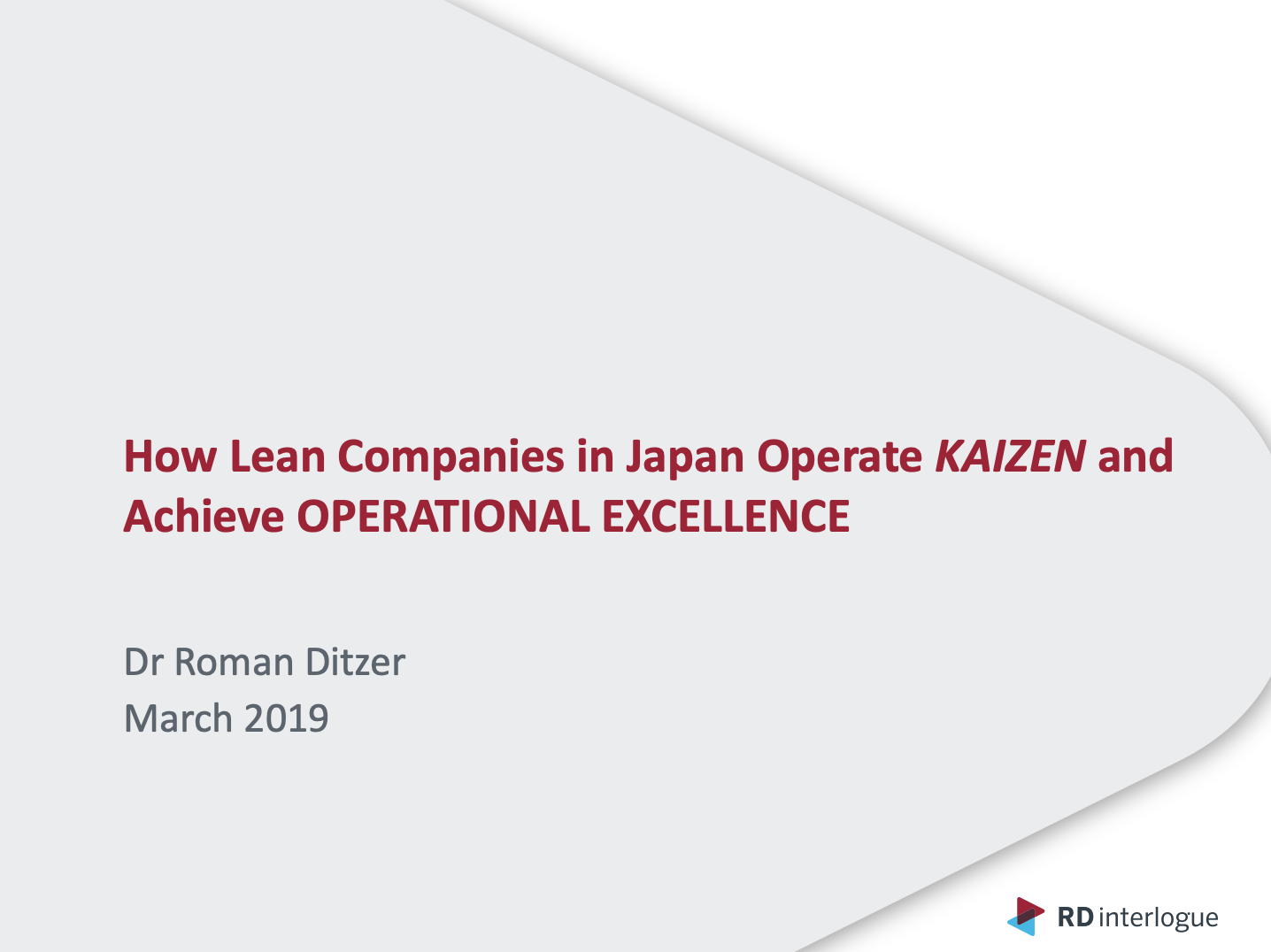