'Mind Shifter'
This term denotes texts which stimulate brain functions and other activities. You can find them here.
ON LEAN PRODUCTION, OPERATIONAL EXCELLENCE AND MORE
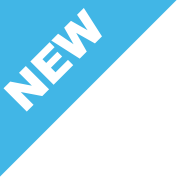
December 2023
What's LEAN Got To Do With It: Lean Management / Lean Leadership – A Cursory Perspective on Global Research and the Practice in Japan (2023)
Although management and leadership are generally differentiated from one another, research has long since done away with this distinction: "instead of distinguishing managers from leaders, we should be seeing managers as leaders, and leadership as management practiced well." (Henry Mintzberg). And indeed, more often than not managers are also leaders at the same time. How should this be seen in the context of Lean Management / Lean Leadership? Is there a successful lean leadership style? And what characterises it? Scientists and managers provide answers to these questions. In a short article, the tasks of a manager-leader in a lean organisation are divided into four areas and these are described. Quotes from the literature and from practitioners in Japan illustrate the approach and self-image of managers in Japanese lean organisations. This shows that against the background of a holistic understanding of Lean as an improvement system, managers must master a wide range of tools.

May 2021
TESSEI: The '7-Minute Miracle' – An Insight into the Realisation of the 'Shinkansen Theatre' (2021)
This article is a rare example of a text written by a top manager looking back and describing his leadership philosophy and approach in a turn-around project. TESSEI is a subsidiary of East Japan Railway Company (JR-EAST) and responsible for the cleaning of the Shinkansen carriages at the Tokyo Station terminus – all in the space of just a few minutes before the trains set off again. During his time at TESSEI, the author succeeded in reforming the company and bringing about a revolution in its corporate culture. Along the way, it was possible to improve and consistently standardise the work processes. Looking back, he feels that the biggest hurdle was the attitude of the staff. The breakthrough came by changing this attitude. The company enjoys cult status in Japan and is famous beyond the borders of the country.

"This 'shifter' certainly struck a chord with me. Because it encapsulates something we realised at DB Systel: The first step towards quality and recognition is healthy self-confidence and an awareness of the value of one's own work. Without this self-confidence, anything you try to set in motion will grind to a halt. At DB Systel, we were the much-maligned IT service provider for Deutsche Bahn (German Railway). And we, like everyone else, had internalised the idea if the IT wasn't working again, then it must be our fault...
(Read more)
This 'shifter' certainly struck a chord with me. Because it encapsulates something we realised at DB Systel: The first step towards quality and recognition is healthy self-confidence and an awareness of the value of one's own work. Without this self-confidence, anything you try to set in motion will grind to a halt. At DB Systel, we were the much-maligned IT service provider for Deutsche Bahn (German Railway). And we, like everyone else, had internalised the idea if the IT wasn't working again, then it must be our fault.
Six years ago, when we set out to fundamentally transform ourselves, one of the eight initiatives was called 'Image'. I was responsible for the change process at the time and was finding it quite difficult: How can we change our 'image' before we significantly improve our performance? But I realised that if we hadn't first held our heads up high, put our backs into it, looked our clients at Deutsche Bahn in the face, and said: 'Yes, we believe we can achieve something. We will master the complexity of the railway system together with you. We will rise to the challenges of digitalising the railway. And we will work with you to navigate the complications that will undoubtedly arise!' then all the fundamental changes, modernisation and improvements that have since followed would never have happened. Because what was at stake was the dignity of the people at DB Systel, and this had to be restored first of all.
I'll never forget the meeting we had in 2016 with around a thousand top managers from Deutsche Bahn: the person leading our 'Image' initiative had insisted that we in attendance from DB Systel should all wear a tie with the DB Systel logo on it. Again, I had my doubts. Put simply, I was embarrassed. And again I had to learn: the feedback was - respectful! Everyone, even very critical clients, appreciated the fact that we were showing our faces. And on the second day of the event, Reiner Grube, then CEO of Deutsche Bahn, stood on the stage wearing one of our ties and paid tribute to our commitment to the railway. The impact on the inside was even more profound: Management was no longer ashamed of their company. Complaints from clients were no longer simply 'passed down' through the hierarchy. Instead, management stood in solidarity with their own staff, making a noticeable effort to initiate solution-orientated dialogue processes whenever clients escalated. The key thing, however, was actually the signal: We in the management team believe that you do good work, we believe that you have great skills, and we believe that the railway needs you. This confidence, this empowerment, set many things in motion: new types of innovation processes, as well as a revolution in managerial work towards self-organisation and agility. And the process continues to this day.
DB Systel has doubled its turnover to €1.2 billion. And in a tight recruitment market, it has increased its workforce of IT experts for the railway from 3,600 to over 5,000. The company regards itself nowadays as a digital partner for the railway, always on an equal footing with its clients. Employees now take this feeling for granted. But that wasn't the case six years ago. The wonderful story of TESSEI and TERUO YABE made me realise what actually happened back then: Yes, the dignity of the employees was restored - and a fascinating process of change was then allowed to unfold, the energy of which is still far from exhausted today, some six years later!" "
2019
World Class – Realising a Dream and Reviving a Plant – The Alternative: Demise (2019)
A Japanese top manager takes stock of over 40 years of genba experience: What are the factors for success in improving and implementing lean? He presents his findings as the top manager of a production plant that under his leadership underwent a dramatic change. This article is a rare example of a text written by a top manager looking back and describing his leadership philosophy and approach in a turn-around project. It is also a valuable tool for understanding the managerial role in kaizen companies in Japan. Many organisations in Germany and Europe are on the lookout for ways to be more effective in their improvement activities. This text has significance beyond the case described herein.

2014
Pars pro toto – The Toyota Production System as Part of an Integrated Model of Corporate Management (2014)
In the midst of a worldwide boom, the Toyota Production System (TPS) has long since transcended the confines of the automotive industry as a blueprint for how to organise value-added processes. TPS used to be thought of as simply a concept and an instrument for designing and improving production processes. However, the focus on production is not sufficient in itself to explain Toyota's success in manufacturing excellence and making continuous improvements. Rather, one should examine the close relationship between the production concept and various other factors and practices, which goes beyond the strict definition of a production system. In this article, TPS finds its place in a production-wide system of corporate management.
